MIG WELDING GAS: OVERVIEW AND CATEGORIES
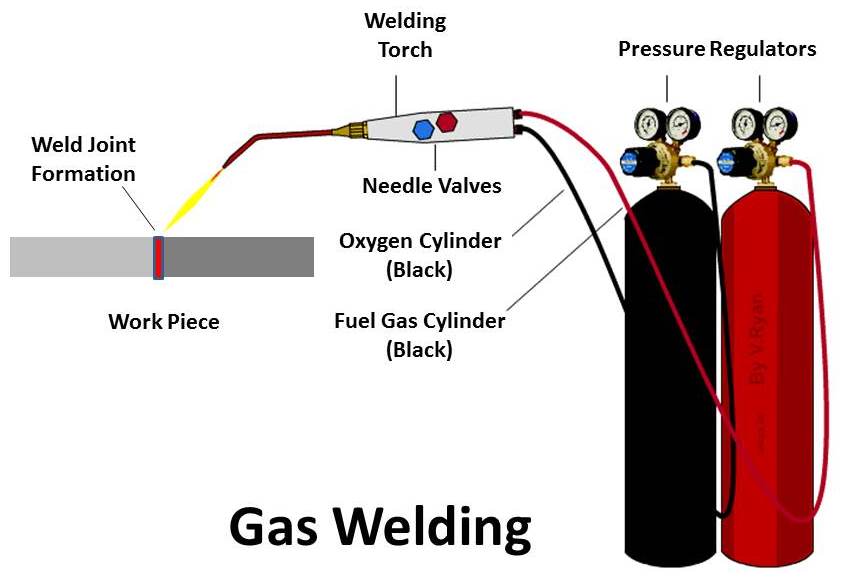
Mig welding gas is essential and required to keep oxygen away from the weld pool. The shielding gas replaces oxygen-rich air that surrounds the weld pool.
Categories:
This gas mainly falls into two categories
- Inert and
- Active
Inert means that gas will not affect whatsoever over the welding process. And Active, as one might guess, has some notable effect on the process.
Now about the types of Active and Inert welding gas:
Argon in Welding:
Argon is often the most used inert gas and is widely used in the production/ fabrication of metals.
It is available in both cryogenic liquid form and compressed gas. It remains in this Inert state at all pressures and temperatures. When compared to other gases, it has lower rates of thermal conductivity.
It is a shielding gas used for Tig and Mig welding. A mixture of Co2 and Argon is often made use of in Active Mig welding gas. Pure Co2 is also helpful in the process. Active gases are employed for most metals, except when it comes to Mig brazing and Aluminum, where Argon becomes useful.
Apart from welding, Argon is used in plasma cutting and in paints to keep away moisture and oxygen.
Co2 in Welding:
Co2 costs the least when it comes to active gases. But that does not mean it is the best that is available. While it can produce a cooler weld, it is coarser and makes a splattery arc with a harder weld. It is challenging to work with this gas on thin materials, and not all welders can perform efficiently with Co2 as shielding gas.
A mixture of Co2 and Argon can provide superior results. It presents a softer arc and smoother process. It results in a weld that is more malleable compared to the case where pure Co2 is employed.
The Types of mixes of These two gases for Mig welding in Australia are:
- 80% argon and 20% Co2- 20mm plus steel.
- 90% Argon and 10% Co2- 25mm steel
- 95% argon and 5% Co2- 10mm steel
What are the effects of Inert and Active Gas in Welding?
In Mig welding, inert gas like Argon will have no effect or reaction. It merely performs the function of replacing the oxygen present around the weld pool.
Active gases have a significant impact on the welding process. It has a two-fold effect:-
- The mix of Argon + Co2 makes it conduct electrically slightly better. This effect, in turn, increases the arc voltage, which further increases the rate of penetration.
- Co2 can break down the surface tension that a molten weld pool possesses. It is the same kind of surface tension that allows water to form drops.
When one uses Co2 to break this tension in the weld pool, it allows the weld to flow smoothly and flatten adequately to create the required weld profile.
If one uses an inert gas for Mig welding (not in Aluminium and Mig brazing), higher machine power is crucial to achieving the required penetration. Also, remember that the finished weld will appear much taller as the surface tension is not broken.
Mig welding & Mag Welding:
Because active gases are used in several Mig welding processes, most operators are technically MAG welding. It stands for Metal Active gases. MIG (which means Metal Inert Gas), over the years, has become the more generic term although, it is not essentially the correct usage.
Industrial welding gases are also available in cylinders for large-scale use.